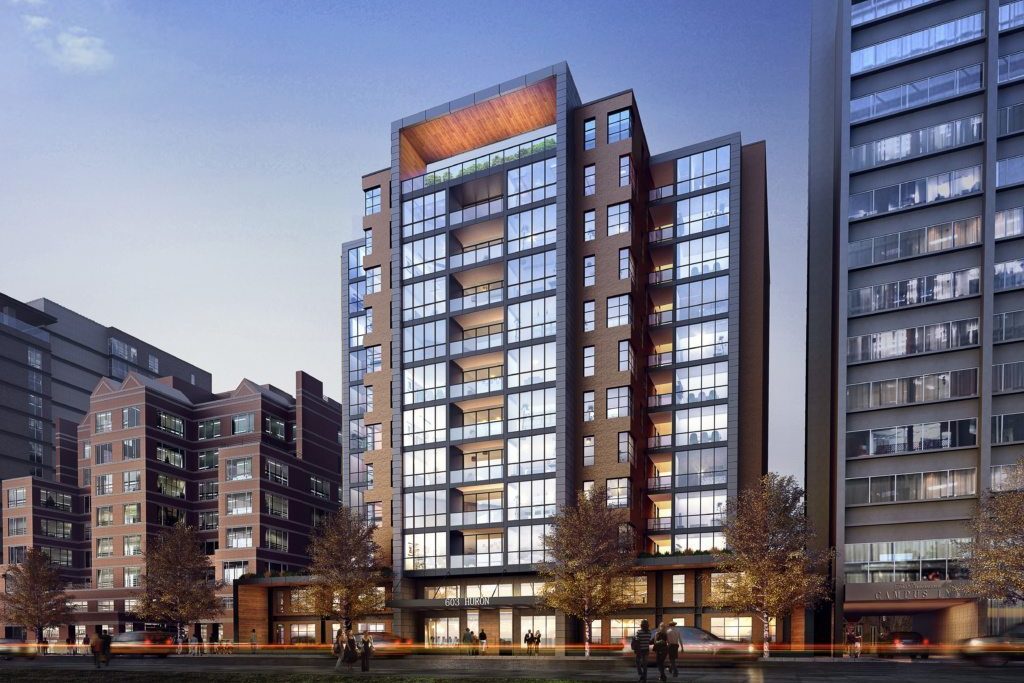
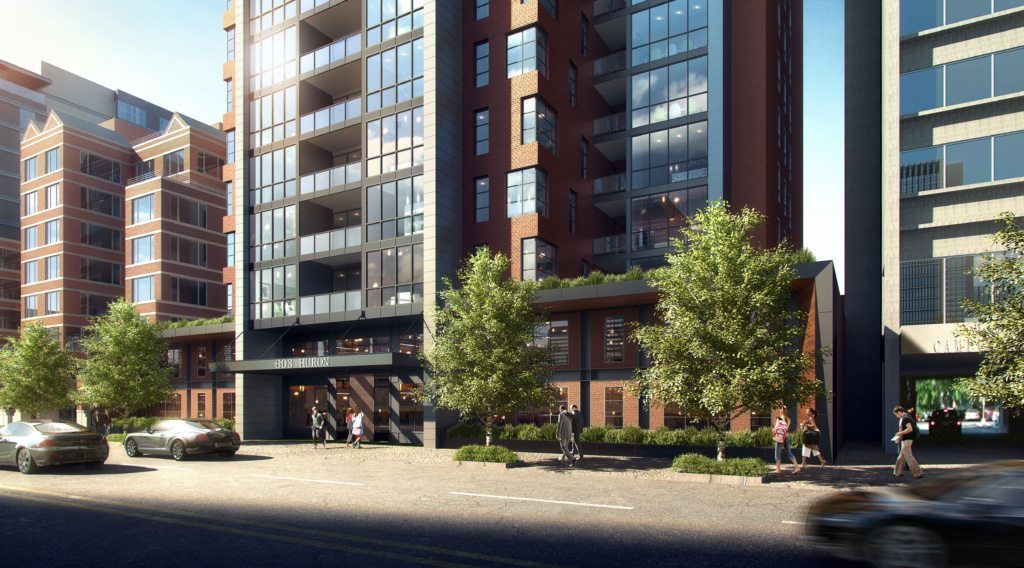
Renderings courtesy of Myefski Architects
SERVICES
Mechanical
Electrical
Plumbing
Fire Protection
SIZE
131,181 SF
CLIENT
Myefski Architects
ANN ARBOR, MI
RTM provided MEP/FP engineering for a new 131,181-square-foot, 12-story, 124-unit residential complex in the heart of Ann Arbor, MI, and within walking distance to the University of Michigan. The complex accommodates a variety of layouts, including studios, two-, three-, and four-bedroom options, and multiple amenity spaces such as a club room, fitness center, spa, business center, an outdoor terrace, and rooftop lounge area with an infinity hot tub and fireplace. A two-level, 34,244-square-foot underground parking garage can house 85 vehicles with an additional 23 surface-level spaces on site.
One of the top priorities for the building was sustainability as Ann Arbor requires projects to meet a certain minimum in terms of energy efficiency. Various electrical and mechanical design factors were taken into consideration to meet this standard. For example, energy-efficient LED lighting fixtures were installed throughout the building. Additionally, RTM utilized a water source heat pump for the primary heating and cooling of the building, which includes a hydronic loop being tempered by a cooling tower and condensing boiler system.
This design is the most energy efficient for a building of this size because it allows for the exchange of unwanted heat in one space, such as warm air during the summer months, and utilizes it in other areas, such as heating for domestic water usage. The loop design minimizes the use of the boiler and cooling tower to provide a highly effective mechanical system.
Ventilation is provided from a make-up air unit on the roof, which had to be custom built to meet the height requirements of the project site. As a result, RTM was able to modify the equipment to maximize its efficiency and to accommodate the various pressure imbalances within a high-rise building such as stack effect, wind effect and piston effect. RTM completed calculations to determine the extent of these imbalances and applied solutions to offset them by pressurizing spaces where needed. A stairwell and elevator pressurization system also was designed for this project to meet the requirements of the building code and to positively pressurize the elevator shaft and stairwell in the event of a fire occurring within the building.