FEATURES OF INDUSTRIAL BUILDING TYPES
The engineering design of industrial buildings requires an in-depth understanding of their intended use and thorough planning to ensure production time is not lost and the owner’s expectations are met. In addition to providing a safe work environment, factors such as the desired capacity and efficiency of the facility, a floor plan that anticipates future growth, ceiling height, ventilation, and lighting, are all important considerations.
Manufacturing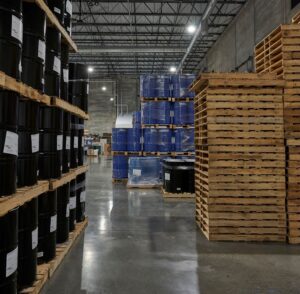
Manufacturing facilities are designed to house equipment used to produce goods or materials. These facilities tend to need a large space for production equipment and multiple docks for trucks to receive materials and ship finished products. RTM designs the systems not only for the core and shell of these facilities, but also for the internal systems, such as conveyors, cranes, and automated storage and retrieval systems. RTM’s experience includes FDA-regulated food processing facilities, and our design approach reflects a thorough understanding of industry regulations.
Storage and Distribution
Storage and distribution buildings provide a space to store and transport goods from one location to end consumers. These buildings tend to be single-story with multiple loading docks. Cold storage buildings in particular are designed to hold large-capacity coolers and freezers. RTM understands the role of refrigeration in maintaining product quality, meeting FDA or USDA requirements, and protecting workers through process safety management. We evaluate energy consumption, first costs, expandability, and user interface in selecting the right type of refrigerant and equipment. Each design will vary with complexity, redundancy, and temperature and humidity requirements, and we treat each project as critical for quality control.
Flex Space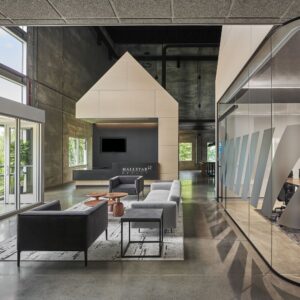
Flex space, or light industrial buildings feature office, production, and storage spaces all in one facility. These buildings often house R&D companies, data center equipment, or showroom displays. As engineering consultants, we evaluate the owner’s needs, understand growth plans, discuss budget, and create an efficient and reliable process for our clients.
CASE STUDY: PETOSKEY PLASTICS | MCKINNEY, TX
RTM is serving as the Prime Consultant, leading the design team through a multi-phase renovation, tenant improvement, and expansion of an existing manufacturing facility for Petoskey Plastics.
RTM provided mechanical, electrical, plumbing, fire protection, construction administration, commissioning, and civil engineering services for Phase I. This included the addition of a new office area to the warehouse, and a 70-foot tower to house equipment for the blow film extrusion. Phase I scope also included the design for industrial ventilation, chilled water, compressed air, and electrical power systems to support their blown film production lines. In addition, RTM designed modifications to the existing fire sprinkler system to protect the new 70-foot tower, including adding a fire pump.
RTM’s civil team provided an array of services for Phase I of the project including design for the water, wastewater, and stormwater systems, as well as land planning and site development. Phase I involved mapping out and analyzing the existing flood zone to ensure that severe impacts from site improvements could be avoided. Due to the fast-tracked schedule, many of the civil services were subdivided into more manageable phases and often occurred at the same time as construction.
With Phase I complete, and Phase II in the preplanning stage, the end result will be an estimated 130,000-square-foot facility over the next five years.
Our team worked closely with Petoskey Plastics to learn about their manufacturing processes and requirements so that the MEP/FP systems were designed to support them.
The design for the facility began in February of 2021 with the first phase completed in 2022. This required the team to fast track the project schedule through design, permitting, and construction, while quickly addressing and redesigning utility coordination conflicts discovered during construction. With pandemic related restrictions and material and labor shortages, teamwork and communication across all disciplines was crucial. Phase II is currently in the preplanning stage and our team continues to be flexible and responsive to support the owner’s expansion goals.
Petoskey Plastics has facilities in Michigan, Indiana, Tennessee, and Texas with more than 650,000 square feet of manufacturing space, serving more than 30 Fortune 500 companies.
Petoskey Plastics is an environmentally focused recycler and plastic film, bag, and resin manufacturer. They provide products and engineered solutions for a variety of industries including automotive, industrial, institutional, retail, construction, home improvement, and medical. This new facility will allow the company to increase their ability to service current customers as well as add new opportunities for their growing sustainable product lines.